Improved Alignment
Research has verified that increasing the available power during reflow has two significant effects:
- Increased Power availability reduces the necessary air temperature needed to Reflow.
- A reduction in Reflow Temperature results in higher solder viscosity, producing improved alignment characteristics for BGA and SMT components.
These two important effects produce the following important advantages:
- Reduced component and board stress
- Prevent the possibility of scorching
- Assist in the prevention of bridging between contacts
- Help align BGA components more comfortably
Linear Air Delivery
The Heat Acceleration Chamber and delivery Nozzle Block are designed to provide maximum air spin of the air flow to the nozzle, ensuring minimal temperature differences across wide area packages, important for linear reflow of CCBGA and larger devices.
Flo-Master-Z Order Information:
- 5000-2000-Z Flo-Master 110v Z-Axis Unit Includes: Power Supply 110v, Reflow Head with 2.500″ of Z-Axis travel (1200watts), Integrated Localized Pre-Heat System (600watts), Digital Controller with all 4 modes of operation, 8″ x 12″ Frame Holder on linear rails, Self-Contained Vacuum IC removal device, SMD Tool Kit, Halogen Light w/ mounting bracket, Chipmaster T and Sniper Demonstration video, Foot Pedal, Power Cord, three user-selected Reflow nozzles, and two user selected pre-heat nozzles.
- 5000-2002-Z Flo-Master 220v Z-Axis Unit Includes: Power Supply 220v, Reflow Head with 2.500″ of Z-Axis travel (1200watts), Integrated Localized Pre-Heat System (1200watts), Digital Controller with all 4 modes of operation, 8″ x 12″ Frame Holder on linear rails, Self-Contained Vacuum IC removal device, SMD Tool Kit, Halogen Light w/ mounting bracket, Chipmaster T and Sniper Demonstration video, Foot Pedal, Power Cord, three user-selected Reflow nozzles, and two user selected pre-heat nozzles.
|
Benefits:
- Enables true reverse manufacture rework
- Low Temperature removal of components
- Maintains integrity of existing solder
- Automatic removal of components at eutectic stage
- All types of PCB products accommodated
- Total area, simultaneous reflow of component
- Run continuous or pulsed
- Rework soft plastics and sensitive components requiring short heat cycles.
APE also offers video narrated trials to help in the evaluation process, our lab technicians will perform your job and return the completed work with the video.
Specifications:
- Power: 110V-1800 Watts, 220VÐ2400 Watts
- Current: 16.36 Amps @ 110V, 10.91 Amps @ 220V
- Dimension: 26″ x 12.75″ x 16″ (660 x 324 x 406 mm)
- Board Holder: Standard 8″x12″ (203 x 304 mm)
- 3 Reflow Nozzles included: (User may select alternatives)
- 2 Preheat Nozzles:
- Air Velocity: (Both Heaters) <12.7 CFM
- Vacuum: Internal (Optional factory Air)
- Air Source: Internal
- Controller (Both Heaters): Fuzzy logic PID Profile Storage
- 4-Axis X-Y Table Built In: 19.0″ x 15.50″ (482.6 x 393.7 mm)
- Operation: Pulsed or Continuous
- Maximum Board Size: 32″ x 24″
Preheat
A bottom preheat and in-process heat source, ensures stability of board temperature, reducing the necessary top reflow temperature, thereby following a more precise profile structure for the component undergoing rework.
Temperature Profiles
A range of temperature profiles are installed for bottom and top controllers and each thermal profile may be custom programmed, enabling different combinations of preheat and removal temperatures to be selected.
Mechanical Control
The Flo-Master has been engineered to operate on a standard workbench and includes a built-in X-Y Table for precise alignment. Each of the axis can be locked for optimum control.
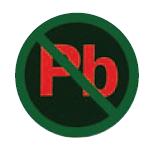
|